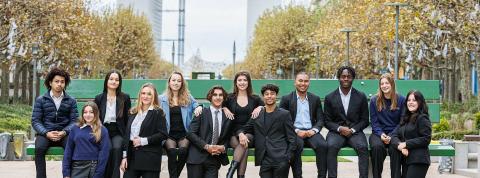
How to analyze direct and indirect costs ?
Analyzing direct and indirect costs is fundamental to optimizing financial management, making informed strategic decisions, and therefore steering a company's profitability. Understanding the nature of these costs, knowing how to identify and analyze them correctly can make all the difference. Would you like to acquire these essential skills and much more? Join EDC Paris Business School's Bachelor of Management program, and you'll be perfectly prepared to take on management positions.
What are direct costs?
Direct costs are expenses that can be directly attributed to a specific product, service or project. These costs are easily identifiable and traceable to a particular activity, enabling them to be linked directly to the production of a good or the provision of a service. In other words, direct costs are the expenses required to create a product or provide a service in a concrete, measurable way.
In a manufacturing company, for example, direct costs generally include the raw materials used to make a product. In a furniture factory, for example, wood, screws and nails are considered direct costs because they are required to produce each piece of furniture. Similarly, direct labor, i.e. the wages of employees who work directly on the production of furniture, is another example of a direct cost.
In the service sector, direct costs mainly include the salaries of employees who provide the service directly to customers. For example, in a consulting firm, the fees of consultants who work on a specific customer project are considered direct costs.
Identifying direct costs in the company's accounts is a crucial step towards accurate cost analysis. To do this, it is essential to have a clear understanding of the company's production or service delivery processes. Direct costs are generally recorded in the accounts as variable costs, as they vary according to the level of production or the volume of services provided.
What are indirect costs?
Indirect costs, unlike direct costs, are expenses that cannot be directly attributed to a specific product, service or project. They are necessary to the overall operation of the company, but their link to a particular product or service is less obvious. Indirect costs generally include overheads that support several activities within the organization.
Taking the example of a manufacturing company, indirect costs can include building rent, utilities (such as electricity, heating and water) and administrative staff salaries. For example, the cost of lighting in the factory is an indirect cost because it is not directly linked to the production of a particular product, but is essential to the overall running of the factory.
For a company in the service sector, indirect costs can include marketing expenses, equipment maintenance costs and administrative staff salaries. In a consulting company, costs related to IT infrastructure and administrative support are considered indirect costs, as they support the company's overall projects and activities without being directly attributable to a specific project.
Indirect costs are often recorded as fixed costs, as they do not vary directly with the level of production or volume of services provided, but are essential to maintaining the company's operations.
Methods for analyzing direct and indirect costs
Effective analysis of direct and indirect costs is crucial to optimal financial management and strategic decision-making. Several methods can be used to allocate and analyze these costs, offering different but complementary perspectives.
Cost center approach
The cost center approach consists of grouping indirect costs into specific cost centers, then allocating them to the various products or services according to predefined criteria. Each cost center represents an organizational or functional unit within the company (e.g. production, maintenance, marketing). This method enables us to better understand how indirect costs are distributed within the company, and to identify areas where savings can be made.
Allocation criteria can include surface area occupied, number of working hours, or any other relevant measure. For example, maintenance costs can be allocated on the basis of machine operating hours, while marketing costs can be distributed according to the sales generated by each product.
ABC method (Activity-Based Costing)
The ABC (Activity-Based Costing) method offers a more precise approach to allocating indirect costs. This method identifies the specific activities required to produce goods or provide services, and allocates indirect costs according to the actual use of resources by these activities.
The ABC method consists of several stages:
Identify activities: Determine which activities are essential to the company's operations.
Allocation of costs to activities: Associate indirect costs with the various activities identified.
Determining cost drivers: Identify the factors that influence the cost of activities (e.g. number of orders processed, number of machine hours).
Product or service costing: Allocate activity costs to products or services according to their use of cost drivers.
This method provides a better understanding of the true costs associated with each product or service, and may reveal opportunities for cost reduction or efficiency improvement.
The importance of direct and indirect cost analysis
The analysis of direct and indirect costs plays a crucial role in the financial and strategic management of companies. Not only does it enable us to understand the sources of expenditure, but also to optimize operations and make informed decisions.
One of the main uses of cost analysis is to set prices for products and services. By understanding the direct and indirect costs associated with each product, a company can determine a selling price that not only covers costs, but also ensures an appropriate profit margin. Without accurate analysis, companies risk under-pricing their products, resulting in reduced margins, or over-pricing, which can make their offerings uncompetitive in the marketplace.
In-depth cost analysis enables companies to identify areas where they can reduce expenses and improve profitability. For example, by analyzing indirect costs, a company may discover that certain costs, such as overheads or maintenance costs, can be optimized. By rationalizing these costs, the company can free up financial resources for other strategic investments, or for improving overall profitability.
In addition, understanding direct costs helps control production-related expenses. By closely monitoring material and direct labor costs, a company can ensure that these costs remain under control and do not adversely affect profit margins.
Analysis of direct and indirect costs is also essential for strategic decision-making. It provides a solid basis for assessing the profitability of different products or services, identifying growth opportunities and areas requiring improvement. For example, if a company finds that certain products have disproportionately high indirect costs, it may decide to review its production strategy or discontinue less profitable products.
To learn how to master these skills and successfully navigate the business world, join the Bachelor Management program at EDC Paris Business School and prepare yourself to become a successful professional.